Improving the acetate manufacturing process for sustainability
Commendations, Time for change, Belgium
A leading project by: Celanese (Belgium) Subcategory: Digitalisation & Innovation.
In an ongoing pursuit of continuous improvement and a zero-incident safety, quality, reliability and engagement (SQRE) environment, Celanese Production Belgium B.V. has developed several innovative and digitisation projects across all SQRE areas. These initiatives align with the company’s sustainability objectives, which include supporting customers’ sustainability goals, reducing the use of natural resources, and improving the sustainability of existing products.
Digitising safety work permit issuance
At present, the issuance of safety work permits is entirely paper-based. The company is developing a web API and mobile app to move the complete workflow to a digital platform, including identification and scanning of associated equipment and installations.
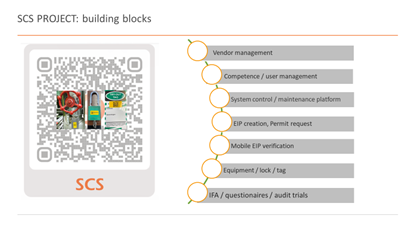
The e-digitisation of the safety work permit process will reduce safety risks, thus lowering the probability of safety and environmental incidents.
This includes hazard and risk assessments, the management of energy isolation activities, monitoring the status of work permits, and completing and following up on checklists.
The effort ultimately supports the company’s objective of achieving a zero EHS incidents/no harm status. The project was initiated in 2022 with an expected completion by December 2024, and will be implemented in several stages, including the execution, training, and go-live.
In-line camera inspection for quality improvement
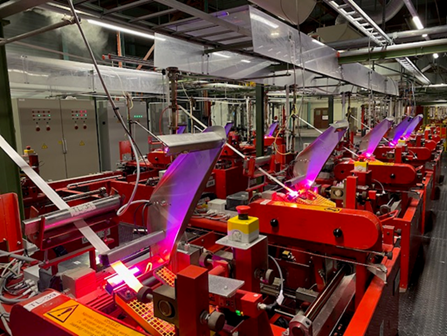
Currently, the quality of the final product, which is continuously produced on multiple lines at high speeds, can only be checked manually by sampling. The ongoing installation of in-line cameras on production lines has enabled the team to implement a continuous monitoring and quality adjustment process.
This will allow for quality improvement, waste reduction and waste recycling optimization, with an anticipated 20% to 40% reduction in waste levels throughout the production process and help the company respond more effectively to potential customer complaints. This part of the project started in February 2023 and is expected to be completed by December 2025.
Spinneret inspection and tracking for more reliability
The Spinneret Inspection and Tracking project involves the development of an automated inspection and tracking system for spinnerets, the devices used to extrude and form acetate fibers. This system includes a robot that feeds the spinnerets to an optical microscope and an API for visualising the output. By improving the inspection and tracking of nozzles, the project aims to optimise and reduce the use of nozzles, positively impacting quality and waste reduction. This part of the project was launched in February 2023 and was completed in April 2024.
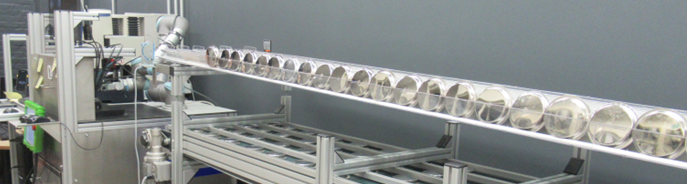
Digital live dashboards and automatic logistics scanning
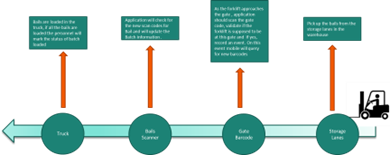
The company also developed several live dashboards to visualise the actual performance of the plant, allowing employees to act faster and improve the quality and quantity of production.
Additionally, the team is developing a software/hardware solution to simplify the logistics and warehousing process, aiming for a more efficient and error-free logistics cycle. The project began in February 2023 and is expected to be completed by September 2025.
These projects collectively contribute to continuously improving processes and serve the objective of achieving zero incidents in the SQRE areas, highlighting the significant potential of innovation and digitisation.
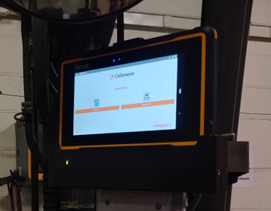
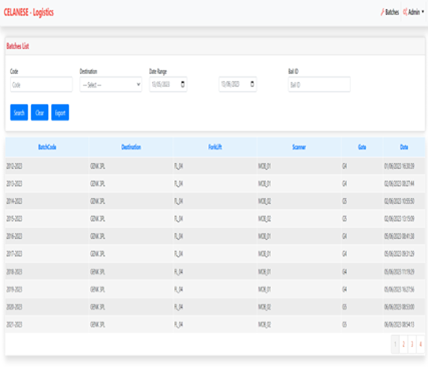
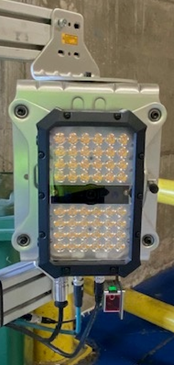
Explore for more information
https://www.celanese.com/ & https://www.celanese.com/en/corporate-sustainability-strategy