Enabling flexible film circularity: from a recyclable full PE barrier packaging solution to a high-end heavy duty sack
Circularity, Belgium
Leading initiative by ExxonMobil.
Seven leading companies, including Hosokawa Alpine, Henkel, Nordmeccanica, Univel, Erema Group, Selene, and ExxonMobil, have collaborated to address the challenge of creating a high oxygen barrier pouch with over 95% mono-material content that’s easy to recycle. Traditionally, multi-material packaging structures excel in oxygen and water barrier performance but are challenging to recycle. This joint effort has yielded a breakthrough—a pouch with exceptional performance that is highly recyclable, promoting circularity in flexible film packaging.
The Challenge
The goal was to develop a high oxygen barrier pouch, consisting of over 95% mono-material, as an alternative to less recyclable multi-material high oxygen barrier laminates. This pouch needed to be recyclable into a high-end film application, promoting circularity in flexible packaging.
The Innovative Solution
- Creating the Pouch: Leveraging the latest polymers and conversion technology, along with a unique collaborative approach, the team achieved a remarkable 96% mono-material PE pouch with high oxygen barrier and excellent package integrity. This blown film used ExxonMobil’s top-quality polyethylene resins, such as Exceed S, Exceed XP, and Exact. It was produced on an Alpine 5-layer line with inline Machine Direction Orientation (MDO) technology, ensuring exceptional film quality, processability, and flatness. Two thin functional layers were added to provide outstanding barrier properties: a 10-nanometer layer of uniform aluminium oxide (AlOx) and a 1-micron layer of Henkel’s newly developed Barrier Coating. Nordmeccanica’s Vacuum & Coating technologies were employed for precise application.
- Printing and Lamination: The film underwent standard Flexo printing by Univel. Subsequently, the MDO-PE was laminated with the sealant web using Henkel’s customised SL Recyclable adhesives on a Nordmeccanica SC 5000 Coating-Laminating machine.
- Recycling: The end-of-life pouches were reprocessed by EREMA, a leader in plastics recycling systems, using their extruder system INTAREMA TVEplus. This produced plastic granules which were used by Selene, experienced in blown extrusion and recycled granules, to create high-quality Form Fill and Seal (FFS) tubulars for Heavy Duty Sacks (HDS).
- Filling and Application: The HDS was filled with EVA resin at the ExxonMobil Meerhout PE production site.
Key Properties of the Pouch:
- Barrier Properties: The pouch maintains a high PE content (96%) while achieving a low Oxygen Transmission Rate (OTR) of approximately 0.14 cm³/m²/d and a Water Vapour Transmission Rate (WVTR) of around 0.6 g/m²/d, comparable to multi-material structures.
- Mechanical Properties: The pouch employs the latest PE resin Exceed S to ensure outstanding package integrity. It offers a 70% improvement in needle puncture energy and force at break compared to similar multi-material alternatives, while maintaining comparable bending stiffness for stand-up capability.
- Optical Properties: The MDO substrate maintains excellent shelf appeal with outstanding gloss (approximately 100%) and low haze (around 4%), rivalling the best-in-class PET substrate.
Recycling Success and Performance
The high barrier pouch was successfully recycled, leading to the production of a new heavy-duty sack film with 50% pouch recyclate in the structure. The result is an HDS bag that, thanks to ExxonMobil PE, meets or even exceeds the performance of industry reference bags. Key properties, including creep, dart, and tear, are comparable to or better than current bags in use at the ExxonMobil Meerhout PE production facility, as demonstrated in Graph 5. Additionally, Table 1 showcases the outstanding bag drop performance, meeting ExxonMobil’s plant specifications and even surpassing expectations in the more demanding ExxonMobil staircase method. This initiative demonstrates the potential for circularity in flexible film packaging, marking a significant step towards sustainable, recyclable solutions in the industry.
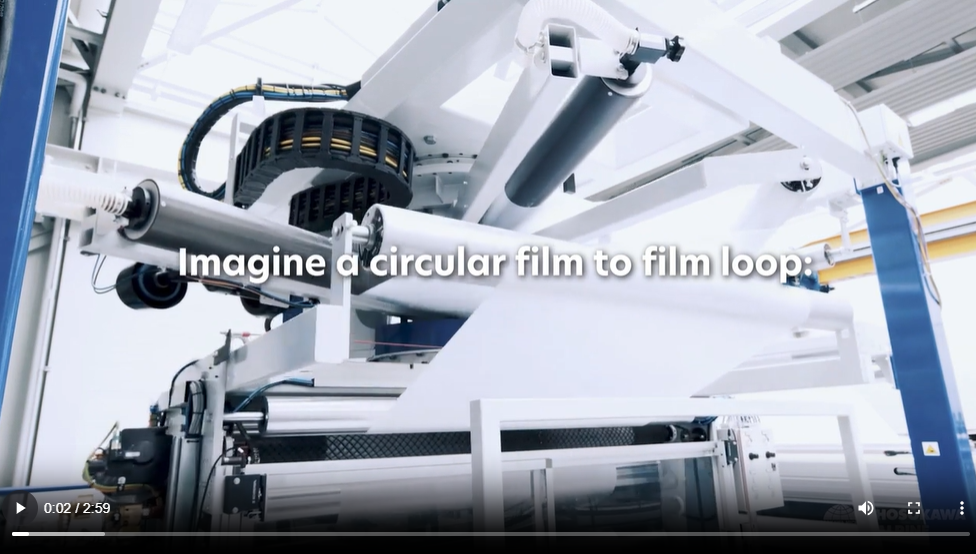