Turning emissions from the steel industry into new products
For 3.5 years, fourteen industry and academic partners from seven countries undertook a joint research project to explore whether CO2 and CO from steel mill gas could be turned into a feedstock for plastics. Amongst them: the chemical company Covestro, the insulation company Recticel, the steel producer ArcelorMittal, and the University of Ghent.
Steel blast furnace gases include CO2 and CO, which has a higher energy level than CO2 and therefore requires less energy than CO2 to be turned into chemicals. The Carbon4PUR consortium has developed and demonstrated a novel process based on direct chemical conversion of mixed CO/CO2 streams from steel blast furnace, avoiding expensive physical separation, thus, substantially reducing the carbon footprint, and also contributing to high monetary savings.
Results
The project came to its conclusion in March 2021: The technology the group unveiled is indeed feasible, both ecologically and economically. It has demonstrated the production of novel polyols from blast furnace gases from steel production which can be used as a valuable carbon source for plastics. Polyols in turn are used to produce polyurethane for mattresses.
The insights from this study have allowed Covestro to develop a plastic with Recticel, that is based on 20% recycled CO2. This plastic is already being used today for the production of foam mattresses, binding material for sports floors, and elastic fibres.
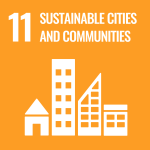

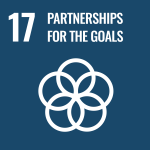