Chemical recycling, a part of the solution for closing the loop
Borealis is driving the transition from a linear to a circular economy. Borealis has developed a strategic framework to move its PO business stepwise towards a circular economy, developing ‘Circular Economy Solutions’ to cover all possible circular offerings for customers, from renewable-based feedstock to chemical recycling. In addition, the Borealis membership of the Ellen MacArthur Foundation’s New Plastics Economy endorses this leading position.

The Borealis circular cascade model is designed to achieve a fully circular economy by combining selected technologies in a complementary and cascading manner. Its goal is to give plastic products multiple lifetimes in the most sustainable way possible. The process starts with optimizing product design for eco-efficiency, re-use, and recycling. Once a product reaches the end of its life, the plastics loop is closed through mechanical recycling, which produces high-value products with low carbon footprint. Chemical recycling is also utilised to further extract value from residual streams that would otherwise be incinerated or sent to landfills. Borealis uses its Borcycle™ recycling technology, including Borcycle M for mechanical recycling and Borcycle C for chemical recycling, to process the valorized materials. These high-quality solutions can be used in more sophisticated applications, such as food packaging and healthcare.
To advance the circular economy, Borealis believes it is essential to develop a chain of custody, paying particular attention to the standardisation of an industry-wide approach to the mass balance model throughout the production process and value chain.
Scaling advanced chemical recycling for circular plastics
ReOil® is OMV’s proprietary chemical recycling technology that converts end-of-life plastics into circular feedstock for the production of chemicals, particularly new plastics. OMV operates at its Schwechat refinery near Vienna and is continuously investing in advancing the technology to ensure a reliable supply of circular feedstock for the market. ReOil® is one of the most advanced and scalable chemical recycling solutions on the market.
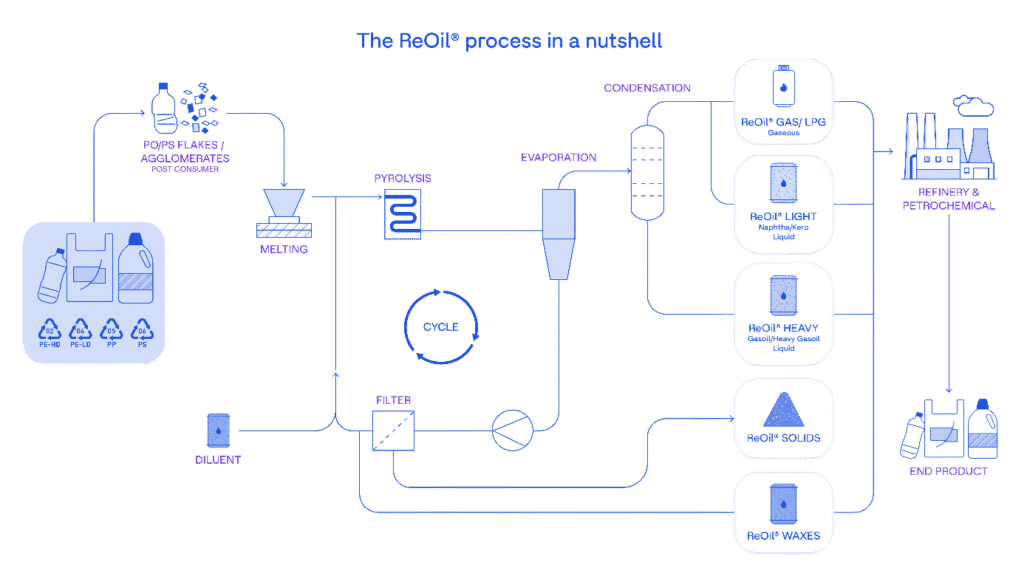