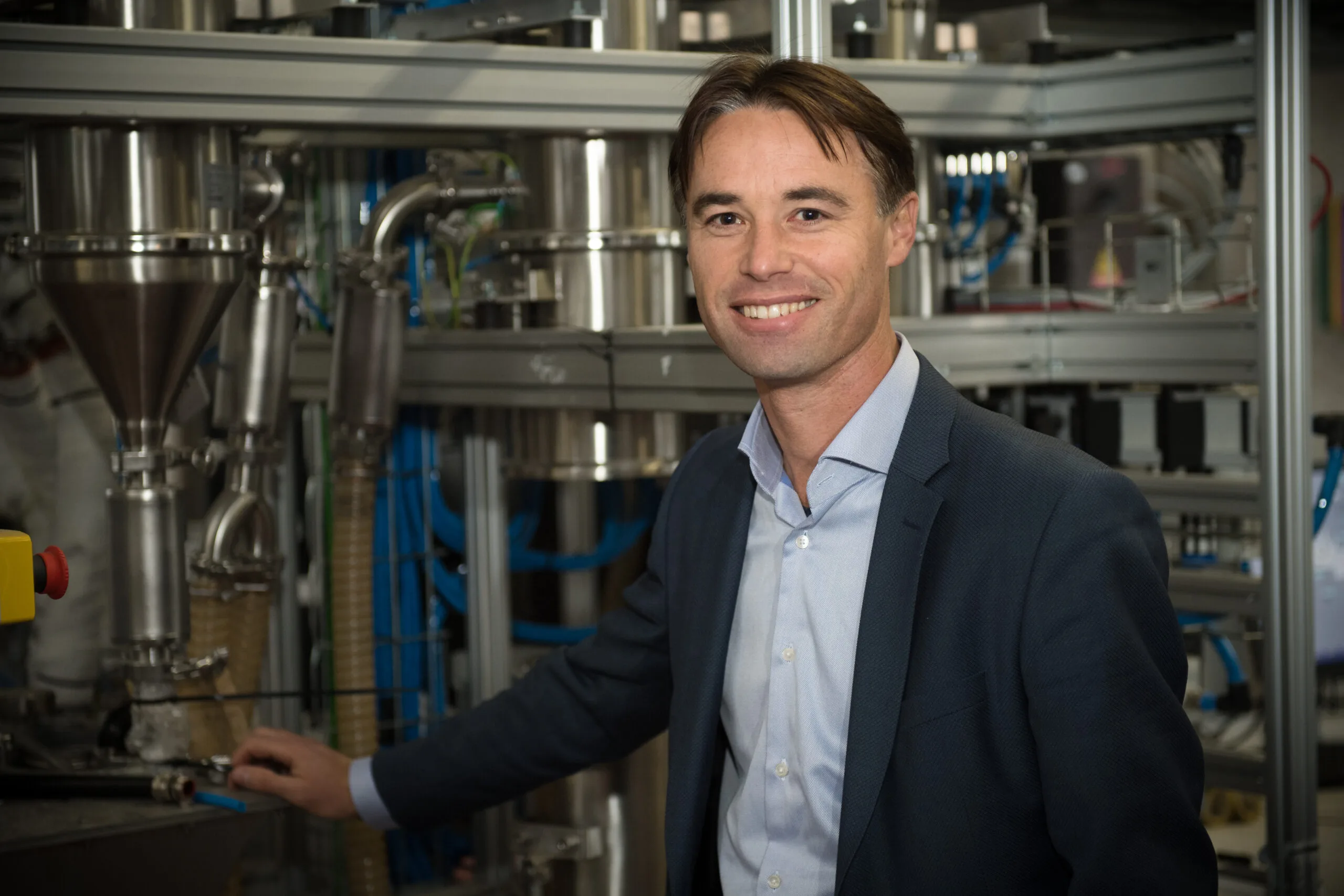
“At Ghent University, we are working on a multitude of chemical recycling technologies because it is our opinion that we will need a combination of different solutions to increase circularity, ranging from gasification to pyrolysis, catalytic solutions and even supercritical conversion. These technologies are complementary to mechanical recycling”,
said Professor Kevin Van Geem from Ghent University.
He shared his insights in a conversation with Cefic, discussing the progress and misconceptions about chemical recycling, and offering his views on the future of these technologies.
In Europe, recycling rates remain relatively low, with only 38% of waste in the EU being recycled (Eurostat, 2022). A rapid scale-up of recycling capacities and infrastructure is critical to meet the EU’s mandatory targets. We need to see plastic waste as a valuable resource and a key element of a circular economy. The idea behind circularity is to establish a continuous cycle, including collection, sorting, recycling and regeneration.
Chemical recycling technology is getting more sophisticated by the day
Studies done by Ghent University, Belgium, indicate that new technologies and strategies are necessary to increase circularity.
According to Professor Van Geem, “the progress that has been made in the field of chemical recycling is enormous”. New recycling pathways have been proposed and are currently being demonstrated at a higher technology readiness level for both polyolefinic and non-polyolefinic waste. “Innovative methods, like the process for recycling polycarbonate, are being developed,” he highlighted.
Efforts are underway to handle unsorted and contaminated waste and process it in ever larger quantities.
Researchers are also working to improve pyrolysis and gasification processes, making them more reliable and reducing contaminants in the final products.
“Active materials and catalysts are also being added to help extract harmful compounds from oils. Catalysts are being developed to completely remove these compounds by hydrotreating the oils”, explained Professor Van Geem. Furthermore, ongoing research involves the exploration of subcritical water and supercritical water processes to address challenges associated with contaminants. Notably, strides have been made in handling common additives found in polymers, such as flame retardants or stabilizers, through meticulous optimization and the selection of optimal operating conditions.
Addressing concerns about the environmental impact of chemical recycling
Energy efficiency of chemical recycling processes is improving too.
Examining whether chemical recycling is too energy-intensive and emits significant amounts of greenhouse gases (GHGs) is crucial for the future of these technologies.
“Gasification and pyrolysis are the processes operated at the highest temperature, but for example gasification can be operated autothermal. To mitigate the environmental impact of this technology, we are presently evaluating electrified designs under the European project Electro. When powered by renewable electricity, these designs yield almost no direct CO2 emissions. Catalysts also play a crucial role in lowering process temperatures, thereby reducing energy consumption”.
On this topic, Professor Van Geem pointed that: “Most people do not even realize that we consume in Europe alone 800 million tons of oil, not even to mention gas. Energy in Europe is responsible for 77.01% of greenhouse gas emissions in 2019, of which transport accounts for about a third. Greenhouse gas emissions from agriculture contribute 10.55%. While industrial processes and product use contribute with 9.10% and the management of waste with 3.32%.”
According to Professor Van Geem, the priority should be on drastically increasing the availability of renewable or low-carbon energy. “The chemical industry can be electrified but as long as there is no electricity available with a low CO2 footprint this makes no sense. Note that we are currently combusting waste on a large scale, which results in considerable direct emissions as shown from the previous numbers. Let’s first stop with that and we will have already an impact”, he added.
We can’t achieve EU recycling goals without chemical recycling methods
Currently, non-mechanically recycled waste is either incinerated or sent to landfills. According to Prof. Van Geem, we need to put an urgent stop on burning valuable resources and shift away from practices like converting waste into electricity.
“Ideally, mechanical recycling is preferred due to its efficiency and minimal energy consumption. This method maintains the polymer structure and avoids chemical transformations. However, it relies on homogeneous, relatively clean waste streams to produce recycled plastics that can match the quality of virgin-grade plastics. Mechanical recycling of plastic waste has been extensively researched, with significant progress over the last five decades. Physical recycling, using solvents and low temperatures to preserve the polymer’s chemical structure, has also seen advancements, including a seven-stage process presented recently. Despite these strides, achieving recycling goals will require a substantial amount of plastics to undergo chemical recycling – breaking down materials into building blocks for secondary raw materials. Currently, chemical recycling constitutes nearly zero percent of total plastic recycling, indicating that the forthcoming decade’s major technological developments and market growth are likely to center around chemical recycling,” Prof. Van Geem explained.
We need to embrace a “design to recycling mindset”. When creating products, the recycling aspects should be included early in the development stage, rather than solely focusing on performance. “For example, think about multilayer packaging. Finding simple methods to separate layers or come up with design of layers with similar materials instead of a multitude of different ones will benefit both mechanical and chemical recycling enormously”, he added.
Europe needs a business case for chemical recycling
In our globalized world, competition emerges from every continent. According to Prof. Van Geem, if a company can make products cheaper elsewhere and import them in a straightforward way, this will happen. It is a potential threat to the chemical industry, similarly as what happened with solar panels. “If the US adopts a free allocation model, it’s crucial to recognize that differing definitions in Europe could divert most investments to the US, stalling progress within Europe.”