A solution to reuse and re-enter waste into product lifecycles by BASF
Most mattresses today are thrown away after an average of 10 years of use, which squanders resources and creates high quantities of waste. In the EU alone this adds up to 30 million mattresses per year. At the same time, valuable raw materials – mattresses – above all crude oil – are needed to manufacture new soft foam. A circular economy solution for mattresses can therefore both reduce waste and save fossil resources.
BASF has developed a chemical recycling process for used mattresses and is starting pilot tests at the Schwarzheide site in Brandenburg, Germany. The materials from old mattresses will be recycled in such a way that they can be used to produce new mattresses. The goal is to recover the recycled materials with a quality that is comparable to virgin raw materials. In doing so, BASF is breaking new ground. It is also responding to the expectations by both the foam and mattress industry and consumers regarding sustainability. This is an important step to re-introduce post-consumer waste into product lifecycles.
How does it work?
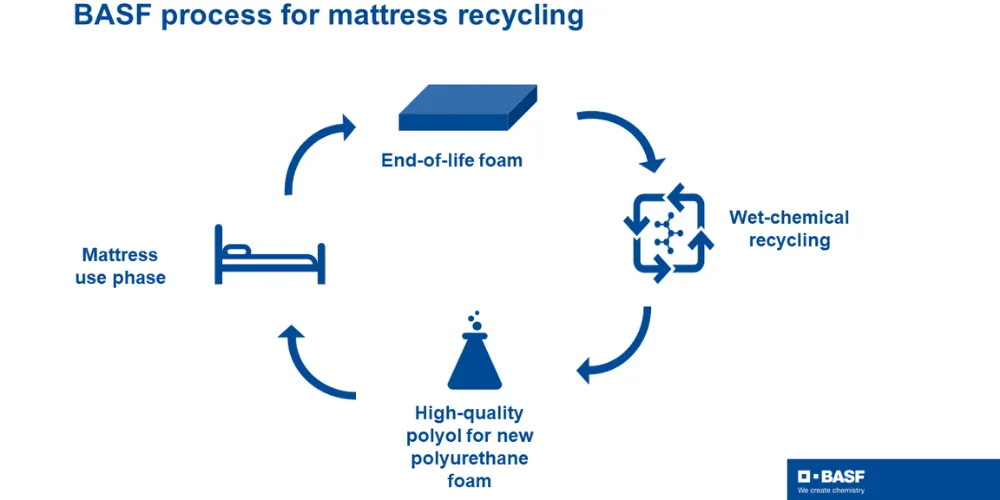
Instead of incinerating or putting mattresses into landfill at the end of their lifecycle, BASF’s process breaks down the flexible polyurethane and delivers the initially used polyol. This is then used as feedstock to produce new foam with a lower carbon footprint since fewer fossil resources are needed. BASF offers a solution to close the loop for polyurethane soft foam with the chemical recycling of mattresses.
BASF’s process breaks down the flexible polyurethane and delivers the initially used polyol. From there, BASF can produce new foam with a lower carbon footprint, because fewer fossil resources are used.
BASF is continuously looking at ways to reuse and re-enter waste into product lifecycles and foster circular economy solutions. With its circular economy concept, BASF aims to decouple economic growth from the use of finite resources and accelerate the adoption of these principles into its day-to-day operations.